November 8th, 2019
6 Weeks on the Road: Approach to Safety
Journalist Chris Heal interviews Harkness, COO David Burlinson to discuss the manufacturing side of the business and the approaches to safety which Harkness puts in place to continually produce high quality products.
CH: Many people in Harkness have had a busy time travelling recently and of course, this article focus on safety so how does travelling to different places help with your work, David?
DB: We learn a lot. It is a continual process. We are a global company and have five manufacturing plants in the UK, France, India, China and one in the USA. We supply over 150 companies around the world. On our business travels, we visit manufacturing plants, suppliers and various different companies as well as meeting and listening to customers which means it is a continual learning process.
CH: So for people who don’t know about your role David, how would you sum up your work within Harkness?
DB: My current role is Chief Operations Officer. I am responsible, primarily, for production and quality of our products from all of our five plants. I am heavily involved in material sourcing and quality as well as efficiencies, cost control and basically Mark [Ashcroft], Patrick [Carolan CFO] and David Harrison (CTO) and myself are continually looking at how we can improve, drive the business forward and reduce costs.
CH: You talk about your major involvement with the manufacturing of products so first and foremost, what safety measures do you take at the factory stage?
DB: We take all safety very seriously. We are very proud of our safety record in all of our factories. We have very few to none serious incidents in any of the factories. We have built in safety features in all of the factories and we use up-to-date technology and the latest equipment. We also utilize external consultants to do independent audits on health and safety, who give us recommendations, so we are continually looking at how we can improve although, our safety record is excellent. Visiting individual sites allows local teams to identify new initiatives including those related to health and safety. Learning from the teams is really important and sitting down with them in their own environment is very beneficial.
CH: Do all of those things combined just add to the overall quality of what you are producing?
DB: Yes it does. Quality is first and foremost, and that is pushed down through all of the factory general managers to the supervisors and to the shop floor personnel. We are the world’s leader in manufacturing movie projection screens and we have, in our opinion, the highest quality standard of products in the world. We supply all the Largest Cinema operators in the world – Wanda in China, Dolby, Cineworld, Odeon – so you can’t build up a relationship with those customers and keep it, without both the highest quality products and service.
CH: In terms of the service and efficiency then, they must be key qualities especially when the screens are in transit to these major and leading customers?
DB: We pride ourselves on hitting delivery dates. We try and keep those to a reasonable level which is why we have a global footprint because we believe it is extremely important to be close to our customers. That reduces transit time and import costs for the customer, so that is why we decided to invest in five manufacturing plants around the world. It was a big investment for a company of our size, but we felt it was very important.
It’s all about the customer, gaining customers and keeping them on long term relationship basis. That is, in this day and age, very difficult. You have competitors, price pressures and everything else but we believe that if we get quality and service to the highest standard and we keep it there, then that will retain our customers long term.
CH: The main value for the customers is when the screen is in the theatre so when it arrives, it has to be absolutely perfect when installing the screen…
DB: Everything has to be coordinated and correct. Not only manufacturing the screen, shipping on the day we said we would do, organizing the transportation to get it to the site when the installation team is there and when you have a good installation process, the customer is happy.
Types of packing for screens is continually reviewed depending on whether a screen is subject to dedicated transport or is being trans-shipped. Costs of packing are growing quickly and it’s important we are able to fully understand customer requirements; a few dollars saved on changing the packing might result in the Screen getting damaged.
The quality mantra is all the way through our business. That is our highest priority and that is what we spend the most time, effort and investment on. If we don’t continue to do that and continue to improve, then we will not keep our global footprint and be the number one supplier of movie screens in the world.
CH: You have mentioned the term ‘global footprint’ so are you able to learn from other companies and countries like Japan, in particular?
DB: We utilize a lot of Japanese techniques within the process to continually improve. Things like FMEA – Failure Mode & Effects Analysis, root cause analysis – so basically that means anything you pick up in the plant which has an issue, you identify it down to its true cause and put in new processes, new training and new equipment to eliminate that completely. That is an ongoing process through all of our manufacturing plants.
CH: And one of the ongoing processes which Harkness is continually working on is the environmental sustainability of screens. I know water v solvent is quite a big talking point within the industry so is that something you are involved in with your line of work, David?
DB: We have been doing a lot of work on this over the last four years and it is something we are keen to push.
We’ve actually changed to water-based completely on all of our manufacturing plants over the last four years. Although we had a low level of hazardous air pollutants, we eliminated them completely out of every one of our manufacturing plants. We have been able to reduce our VOC emissions by over 94 per cent over the last four years so we are in a very good place on the coating side for the environment.
We recycle all of our PVC within the plant. Anything which is scrap in the plant goes back to the PVC manufacturer to get it recycled. We’re looking at all of our packaging to see how that can be more environmentally friendly. The latest thing we have been working on is how do we get solar and maybe some wind into our manufacturing plants to cut down our energy bills. That is a large project we are working on right now and I would hope within the next 12 months, we will have at least solar power in every one of our manufacturing plants. We want to continue reducing our carbon footprint.
CH: So do the screens look different with the water-based coating and if so does that effect the performance in anyway?
DB: We utilize thin-film technology which is basically similar to the automotive industry and how they apply the paint on to cars. It creates a smooth, even surface which has very high optical and technical properties. Our products are leading edge in the industry especially our new Clarus products. We have been working very closely with Barco and Christie who are projector supplies and they are endorsing our Clarus products for their RGB laser projectors which is excellent.
Ours do look different from competitors, but I believe our screens are higher quality and have better performance characteristics.
CH: And finally David, Harkness is continuing to lead the way, but how important is it to review, learn and update your manufacturing qualities to stay out in front?
DB: It is a continuous process every day and we are also continually working on new products to bring to the market place which may need different techniques and different equipment, but they will always have the same high-quality standards.
Harkness Screens
Harkness Screens™ is the world’s leading screen technology company, specialising in the design and manufacture of projection screens and supporting technologies for cinema and live events. From single-screen independent theatres to large multiplexes to large format immersive theatre experiences or live events, Harkness supplies thousands of screens every year helping provide outstanding presentation experiences to audiences around the world.
With global reach, Harkness is regarded as the world leader in cinema and has screens in more cinemas worldwide than any other manufacturer. With its industry leading 2D and 3D screen brands (Perlux HiWhite, Clarus XC and Spectral) along with an innovative range of presentation monitoring tools, digital surveying services and suite of cinema design and specification apps, Harkness continues to lead the way in screen technology for cinema.
Founded in 1929, Harkness has manufacturing facilities in the USA, UK, France, India and China and combines unrivalled experience with the latest technology and production methods to provide innovative solutions to the company’s key markets. For more information, visit the Harkness Screens web page at www.harkness-screens.com.
About the writer
Chris Heal – Chrisheal09@gmail.com
Chris is a freelance journalist who graduated from the University of Sunderland with a 2:1 Sports Journalism degree in 2014. Previously having worked as part of the Sky Sports News team, his main focus is not on rugby union.
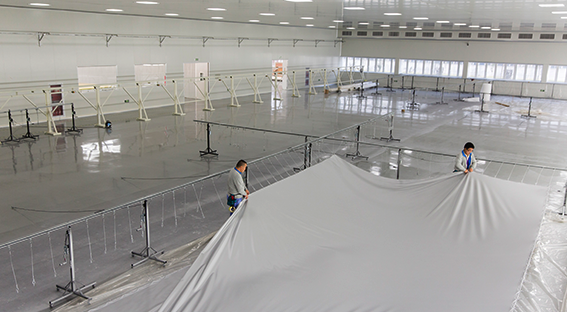